 On eBay Now...
288 page 2006 STEEL & ALUMINUM WELDING Welder Weld Code Combined Manual on CD For Sale

When you click on links to various merchants on this site and make a purchase, this can result in this site earning a commission. Affiliate programs and affiliations include, but are not limited to, the eBay Partner Network.

288 page 2006 STEEL & ALUMINUM WELDING Welder Weld Code Combined Manual on CD: $12.99
Thank you! If you do not wish to have your item(s) delivered on data disc(s), I can provide them on a flash drive and other means as well. Just let me know if a disc does not work for you and we can discuss delivery by other methods. COMBINING SHIPPING COSTS Are you purchasing multiple items? I will: a) combine all invoices before payment and charge shipping equivalent to one item, or b) refund all shipping costs in excess of one item after payment. All derivative (i.e. change in media; by compilation) work from this underlying U.S. Government public domain/public release data is COPYRIGHT © GOVPUBS $3.00 first class shipping in the U.S. and rest of world; combine items to save on shipping charges. Public domain U.S. government manual; not copied from another CD-ROM product.
Numerous illustrations and matrices; see reduced quality examples below.
TITLE:
Ground Combat Vehicle Welding Code - Steel (165 pages)
& Ground Combat Vehicle Welding Code - Aluminum (123 pages)
Published by the Department of the Army in 2006; 288 total pages copied to CD-ROM DESCRIPTION FOR STEEL WELD BOOK:SCOPE: This code contains welding requirements applicable to welding ground combat vehicles, other alloy structures and components. It is to be used in conjunction with appropriate complementary codes or specifications for materials design and construction. It is not intended to supplant codes developed for use in specialized fabrication, such as the ASME Boiler and Pressure Vessel Code, aerospace codes, or military specifications; it is appropriate for use in fabrication of ballistic and non-ballistic primary structures, supporting structures and appurtenances. When conformance to the code is stipulated in contract documents, all provisions of this code shall be complied with, except for those provisions that contract documents specifically exempt.The following is a summary of the code sections and appendices: 1. General Requirements — This section contains basic information on the scope and limitations of the code. 2. Design of Welded Connections — This section has been omitted. Responsibility for this section resides with the design agency. 3. Prequalification — This section contains the requirements for exempting a non-armor Welding Procedure Specification (WPS) from the qualification requirements of this code. 4. Qualification — This section contains the qualification requirements for non-armor WPSs and welding personnel (welders, welding operators and tack welders). 5. Fabrication — This section contains the requirements for the preparation, assembly and workmanship of welded steel structures. 6. Inspection — This section contains criteria for the qualifications and responsibilities of inspectors, acceptance criteria for production welds, and standard procedures for performing visual inspection and NDT (nondestructive testing) 7. Stud Welding — This section contains the requirement for the welding of studs.Appendices Appendix A — Code-Approved Base Materials. This appendix contains tables that cross-reference requirements. Within the type/grade grouping, other materials not specifically listed, may also be used with this document with Engineering approval. Appendix B — Welding of Armor Steel. This appendix contains the welding, testing, procedure qualification, and performance qualification requirements of armor steel. Appendix C — Forms. This appendix contains applicable forms for procedure qualification, performance qualification, and armor welding data sheets. Appendix D — Illustrations – Weld Positions, Test Specimens and Test Fixtures. This appendix contains illustrations displaying dimensional information related to test specimens and fixtures. Appendix E — Prequalified Joint Details and Joint Preparations. This appendix contains the Prequalified WPS limitations.CONTENTSPreface . 3 Introduction . 3 Revisions . 3 Specification Cross Reference . 3 TARDEC/UDLP Weld Team 3 Charter Members. 31 General Requirements. 16 1.1 Scope . 16 Appendices . 16 1.1.1 Application . 16 1.1.2 Limitations 16 1.2 Approval. 16 1.3 Definitions 17 1.4 Welding Symbols. 17 1.5 Equipment Calibration . 17 1.6 Safety Precautions 17 1.7 Standard Units of Measurement. 172 Design of Welded Connections 18 2.1 Intended Use 183 Prequalification of WPSs. 20 3.1 Scope . 20 3.2 Welding Processes 20 3.2.1 Prequalified Processes 20 3.2.2 Other Welding Processes 20 3.3 Base Metal/Filler Metal Combinations 20 3.4 Minimum Preheat and Interpass Temperature Requirements . 20 3.4.1 Base Metal/Thickness Combination . 20 3.4.2 Alternate SAW Preheat and Interpass Temperatures 20 3.4.2.1 Hardness Requirements. 23 3.5 Limitation of WPS Variables . 23 3.5.1 Combination of WPSs . 23 3.6 General WPS Requirements 23 3.6.1 Vertical-Up Welding Requirements 23 3.6.2 Width/Depth Pass Limitation 23 3.7 Common Requirements of Partial and Complete Joint Penetration Groove and Fillet Welds 23 3.7.1 FCAW/GMAW in SMAW Joints 23 3.7.2 Corner Joint Preparation 23 3.7.3 Root Openings. 23 3.7.4 Skewed T Joints 23 3.8 Partial Joint Penetration Requirements. 26 3.8.1 Definition 26 3.8.2 Details (Tubular) 26 3.9 Complete Joint Penetration Groove Weld Requirements 26 3.9.1 J- and U-Groove Preparation . 26 3.9.2 Tubular Butt Joints. 26 3.9.3 Tubular T-, Y-, and K-Connections. 264 Qualification . 28 4.0 Scope . 28 4.1 General. 28 4.1.1 Procedure Qualification Record (PQR) 28 4.1.1.1 Impact Test Requirements 28 4.1.2 Welding Procedure Specification (WPS) 28 4.1.3 Qualification of Welding Procedures 28 4.1.4 Qualification of Welders, Welding Operators, Tack Welders, and Robotic Applications . 29 4.2 Common Requirements for WPS and Welding Personnel Performance Qualificatio . 29 4.2.1 Qualification Responsibility 29 4.2.2 Qualification to Other Codes or Standards 29 4.2.3 Aging 29 4.2.4 Records . 29 4.2.5 Positions of Welds . 29 4.3 General. 34 4.4 Qualification Thickness Limitations. 35 4.5 Qualification Position Limitations 38 4.6 Methods of Testing and Acceptance Criteria 38 4.7 Special Test Weldment Acceptance Criteria . 38 4.8 Groove Test Weldments and Acceptance Criteria 38 4.9 Fillet Test Weldments and Acceptance Criteria 41 4.10 Cladding Test Weldment and Acceptance Criteria . 43 4.11 Hardfacing Test Weldment and Acceptance Criteria 44 4.12 Sheet Metal Weldments and Acceptance Criteria. 46 4.13 Welding Procedure Specification Data 46 4.13.1 Joint Design 47 4.13.2 Base Metal 47 4.13.3 Filler Metal 47 4.13.4 Position . 47 4.13.5 Preheat and Interpass . 47 4.13.6 Heat Treatment. 47 4.13.7 Shielding Gas . 47 4.13.8 Electrical . 47 4.13.9 Variables (see 4.14.9) . 47 4.14 Procedure Qualification Variables 48 4.14.1 Joint Design 48 4.14.2 Base Metal 48 4.14.3 Filler Metals 48 4.14.4 Position . 49 4.14.5 Preheat and Interpass Temperature . 49 4.14.6 Post Weld Heat Treatment 50 1) Omission or inclusion of PWHT. 50 4.14.7 Shielding Gas . 50 4.14.8 Electrical Characteristics . 50 4.15 General. 51 4.16 Testing . 51 4.16.4 Cladding. 53 4.16.5 Hardfacing . 54 4.17 Examination Procedures and Acceptance Criteria. 55 4.17.1 Visual Examination. . 55 4.17.1.1 Test Weldments 55 4.17.2 Radiographic Examination. 55 4.17.3 Bend Tests. 55 4.17.4 Fillet-Weld Bend-Break Tests. 56 4.17.5 Macro Examination 56 4.18 Performance Qualification Variables . 57 4.18.1.1 Welders. 57 4.18.1.2 Welding Operator 575 Fabrication. 64 5.1 Scope . 64 5.2 Base Metal . 64 5.2.1 Specified Base Metal. 64 5.2.2 Base Metal for Weld Tabs, Backing, and Spacers. 64 5.2.2.1 Weld Tabs. 64 5.2.2.2 Backing . 64 5.2.2.3 Spacers. 64 5.3 Welding Consumables and Electrode Requirements. 64 5.3.1 General 64 5.3.1.1 Certification for Electrodes or Electrode-Flux Combinations. 64 5.3.1.2 Suitability of Classification . 64 5.3.1.3 Shielding Gas . 64 5.3.1.4 Storage . 64 5.3.1.5 Electrode Condition 64 5.3.2 SMAW Electrodes . 64 5.3.2.1 SMAW Electrode Storage Conditions . 65 5.3.2.2 Approved Atmospheric Time Periods 65 5.3.2.3 Rebaking Electrodes . 65 5.3.2.4 Electrode Restrictions for ASTM A514 or A517 Steels . 65 5.3.3 SAW Electrodes and Fluxes. 65 5.3.3.1 Electrode-Flux Combination Requirements. 65 5.3.3.2 Condition of Flux. 66 5.3.3.3 Flux Reclamation 66 5.3.4 GMAW/FCAW Electrodes. . 66 5.3.4.1 Low-Alloy Electrodes for GMAW . 66 5.3.4.2 Low-Alloy Electrodes for FCAW 66 5.3.5 GTAW 66 5.5.5.1 Tungsten Electrodes. 66 5.3.5.2 Filler Metal 66 5.4 WPS Variables. 66 5.5 Preheat and Interpass Temperatures. 66 5.6 Backing, Backing Gas, or Inserts . 67 5.7 Backing 67 5.7.1 Fusion. . 67 5.7.2 Full Length Backing. 67 5.7.3 Backing Thickness. 67 5.8 Welding Environment 67 5.8.1 Maximum Wind Velocity . 67 5.8.2 Minimum Ambient Temperature . 67 5.9 Compliance with Design 67 5.10 Preparation of Base Metal . 67 5.11 Tack Welds 67 5.11.1 General Requirements for Tack Welds. . 67 5.11.2 Incorporated Tack Welds . 67 5.11.2.1 Additional Requirements for Tack Welds Incorporated in SAW Welds. 67 5.11.2.2 Unincorporated Tack Welds 68 5.12 Control of Distortion and Shrinkage 68 5.12.1 Procedure and Sequence 68 5.12.2 Sequencing 68 5.12.3 Minimized Restraint. 68 5.12.4 Temperature Limitations 68 5.13 Fillet Weld Assembly . 68 5.14 Technique for Plug and Slot Welds 68 5.14.1 Plug Welds. 68 5.14.1.1 Flat Position 68 5.14.1.2 Vertical Position. . 68 5.14.1.3 Overhead Position 68 5.14.2 Slot Welds 68 5.15 Rework/Repairs. 68 5.15.2.1 Overlap or Excessive Convexity 69 5.15.2.2 Excessive Concavity of Weld or Crater, Under-size Welds, Undercutting 69 5.15.2.3 Excessive Weld Porosity or Incomplete Fusion 69 5.15.2.4 Cracks in Welds 69 5.16 Peening 69 5.16.1 Tools 69 5.17 Caulking. 69 5.18 Arc Strikes . 69 5.19 Weld Cleaning 69 5.19.1 In-Process Cleaning 69 5.19.2 Cleaning of Completed Welds 696 Inspection 70 6.1 General. 70 6.1.3 Inspector Qualification . 70 6.2 Inspection of Welding Procedure Specification and Equipment. 70 6.3 Inspection of Welder, Welding Operator, and Tack Welder Qualifications 70 6.4 Inspection of Work and Records 71 6.5 Obligations of the Contractor . 71 6.6 Nondestructive Testing . 71 6.6.1 Non-Critical Welds. 71 6.6.2 Critical Welds. 71 6.6.3 Ballistic Welds . 72 6.6.4 Procedures 72 6.6.4.1 Radiographic Testing 72 6.6.4.2 Radiation Imaging Systems. 72 6.6.4.3 Ultrasonic Testing. 72 6.6.4.4 Magnetic-Particle Testing. . 72 6.6.4.5 Dye Penetrant Testing 72 6.6.5 Personnel Qualification 72 6.7 General. 74 6.8 Extent of Testing 74 6.9 Radiographic Procedures . 74 6.9.10 Quality of Radiographs. . 76 6.9.11 Density Limitations. . 76 6.10 Acceptability of Welds. 77 6.11 Examination, Report, and Disposition of Radiographs 77 6.12 General. 78 6.12.1 Visual . 78 6.12.2 Liquid Penetrant and Magnetic-Particle . 78 6.12.3. Radiographic . 78 6.12.4 Ultrasonic. 787 Stud Welding 80 7.1 Scope . 80 7.2 Workmanship . 80 7.2.1 Cleanliness 80 7.2.2 Coating Restrictions 80 7.2.3 Base-Metal Preparation. 80 7.2.4 Moisture. 80 7.2.5 Ferrule Condition . 80 7.2.6 Arc Shield Removal . 80 7.2.7 Acceptance Criteria . 80 7.3 Technique 80 7.3.1 Automatic Machine Welding 80 7.3.2 GTAW, GMAW, SMAW Fillet Weld Option. . 80 7.3.2.1 Surfaces 80 7.3.2.2 Stud End . 80 7.3.2.3 Stud Fit (Fillet Welds) 80 7.3.2.4 Fillet Weld Minimum Size 81 7.4 Stud Application Qualification Requirements. 81 7.4.1 Responsibilities for Tests. 81 7.4.2 Preparation of Specimens 81 7.4.2.1 Test Specimens 81 7.4.3 Number of Specimens . 81 7.4.4 Test Required 81 7.4.5 Test Methods. 81 7.4.5.1 Bend Test . 81 7.4.5.2 Torque Test 81 7.4.5.3 Tension Test. 82 7.4.6 Qualification Test Data 82 7.5 Production Control 82 7.5.1 Pre-Production Testing 82 7.5.1.1 Start of Shift 82 7.5.1.2 Production Member Option 82 7.5.1.3 Flash Requirement . 82 7.5.1.4 Bending/Torque Test . 82 7.5.1.5 Event of Failure. 82 7.5.2 Production Welding . 82 7.5.3 Repair of Studs 82 7.5.4 Operator Qualification 82 7.5.5 Removal Area Repair 83APPENDICES. 84 Appendix A Code Approved Base Metals and Filler Metals Requiring Qualification per Section 4 86Appendix B Welding of Armor Steel. 102B1 INTRODUCTION. 104 B1.1 Application . 104 B1.2 Base Metal. 104B2 REFERENCED DOCUMENTS 104 B2.1 Issues of Documents . 104 B2.1.1 Military Documents 104 B2.1.2 Other Publications . 104 B2.1.2.1 American Society for Testing And Materials (ASTM) 104 B2.1.2.2 American Welding Society (AWS) . 104 B2.1.2.3 American National Standards Institute (ANSI) 104B3 REQUIREMENTS 105 B3.1 Weldments. 105 B3.2 Armor . 105 B3.3 Preparation of Welding Procedures and Drawings 105 B3.4 Welders or Welding Operator. 105 B3.4.1 Test Plate Requirements . 105 B3.4.2 Test Plate Acceptance 105 B3.5 Ballistic Requirements . 105 B3.5.1 Heating of Weldments . 105 B3.5.2 Welding Attachments to Armor 105 B3.6 Ballistic Test Plates . 105 B3.6.1 Submission . 105 B3.6.2 Macro Specimens. 106 B3.7 Ballistic Testing Requirements . 106 B3.7.1 Test Plates 106 B3.7.2 Number of Test Plates . 106 B3.7.3 Fabrication of Test Plates 106 B3.7.4 Ballistic Test Requirements . 110 B3.7.5 Ballistic Testing. 110 B3.7.6 Test Method 110 B3.7.7 Evaluation of Test Results. 111 B3.7.8 Visual Examination of Test Plates . 112 B3.7.9 Radiographic Inspection of the Test Plate. 112 B3.7.10 Repair of Test Plate . 112 B3.7.11 Rejection of Ballistic Test Plate . 112 B3.7.12 Retests 112 B3.8 Radiographic Procedure 112 B3.8.1 Radiographic Drawings . 112 B3.8.2 First Production Weldment 113 B3.9 Inspection of Production Weldments 113 B3.9.1 Visual Inspection 113 B3.9.2 Radiographic Inspection 113 B3.9.3 Alternative Testing 113 B3.9.4 Inspection of Weldments Subjected to Straightening 114 B3.9.5 Marking of Repairs to Weldments . 114 B3.9.6 Quality Control 114Appendix C Forms . 116Appendix D Illustrations — Stud Weld Positions, Weld Test Specimens and Test Fixtures 128 D1 Standard Stud Test Weldment Positions. 130 D2 Guided Bend Specimens. 130 D2.1 Preparation of Groove weld Specimens. 130 D2.3 Subsize Transverse Face and Root Bends 130 D2.4 Nonstandard Bend Specimens. 130 D3 Tension Specimens . 130 D4 Cladding and Hardfacing Specimens. 130 D5 Test Fixtures 130Appendix E Prequalified Joint Preparations and Joint Details 144
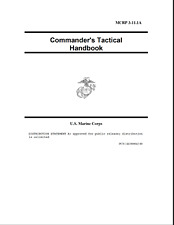
288 Page 1998 MCRP 3-11.1A USMC Marine Corps Commander’s Tactical Handbook on CD $12.99
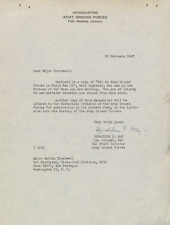
288 Page Women's Army Auxiliary Corps WAC Ground Forces WWII History on Data CD $14.99

Incredible Hulk 288 SPLASH PAGE pg 1 ORIGINAL ART signed sal BUSCEMA 1983 $9500.00
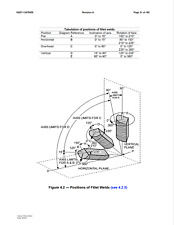
288 page 2006 STEEL & ALUMINUM WELDING Welder Weld Code Combined Manual on CD $12.99

Iron Man #288 VF Marvel 1993 "48 Page Anniversary Special" I Combine Shipping $2.85
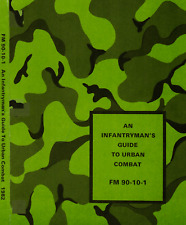
288 Page 1982 FM 90-10-1 Infantryman Guide Urban Combat MOUT Close on Data CD $14.99

288 Page 40th Bombardment Group 1944-1945 AAF History India China on Data CD $14.99

288 Page 1955 F9F-5 Panther AN 01-85FGC-1 Pilot's Handbook Flight Manual on CD $19.99
|